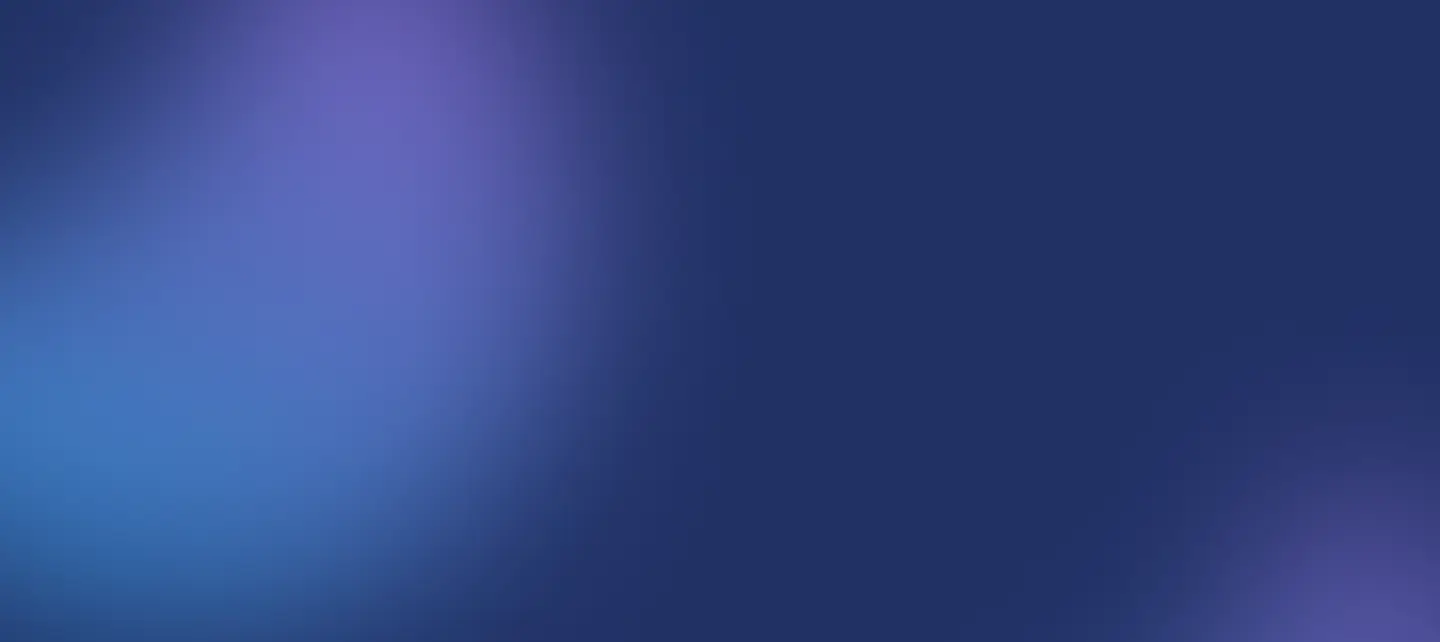
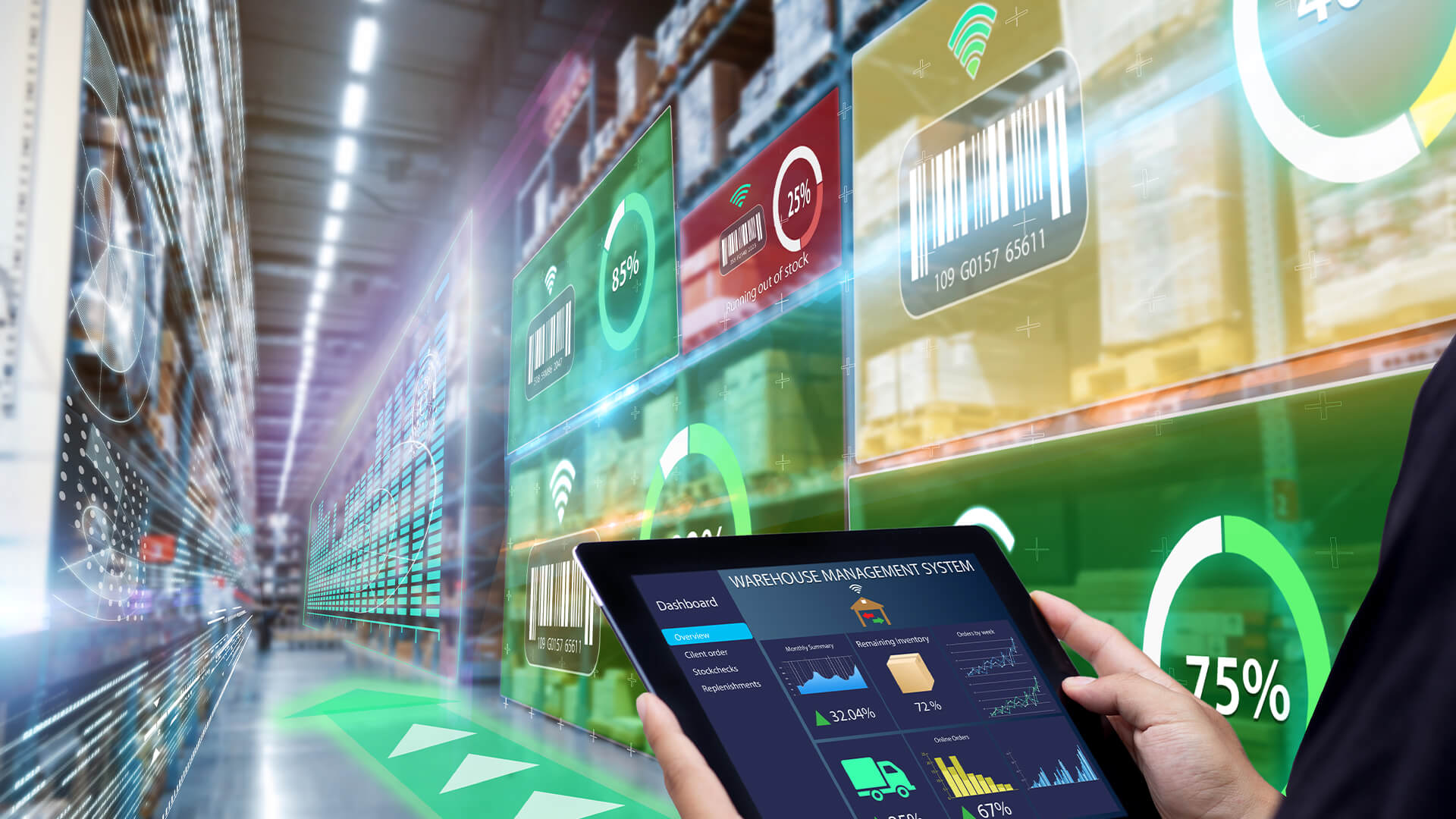
The warehouse is undergoing a huge transformation, from repository to fulfilment powerhouse, but there are risks to growth that need to be addressed. Robotics, AI and digitalisation could hold the key to boosting capacity. By Craig Whitehouse and Tim Wright, Managing Directors at Invar Group.
What is the shape of modern warehousing and where is it heading? Far from its traditional role as a repository for inventory, the warehouse has become a powerhouse for fulfilment, whether it be replenishing retail stores, feeding just-in-time manufacturing lines or serving a discerning customer base directly through ecommerce.
Demands placed upon the performance of the warehouse have ratcheted up considerably over the past ten years as C-suite decision makers have come to realise the critical role the warehouse plays in delivering on the ‘customer promise’, developing market reach and strengthening the competitive position of the business.
Immediacy is now a commercial imperative. Sales can be won or lost on availability, speed of despatch and proximity to the customer. Short lead-times and late cut-offs play a decisive role in winning and retaining customers – and margins, along with brand reputation, can be enhanced or diminished by the speed and efficiency with which returns are processed and refunds managed.
Warehouses are fast becoming ‘fulfilment factories’, increasingly mechanised, automated and digitally integrated with the wider supply chain. The future looks bright, but there are significant influences and challenges that business will need to consider and act upon in order to mitigate rising costs, protect margins and increase capacity.
Costs on the rise
Rising costs are an immediate concern with energy prices spiking, wages increasing and container shipping rates – although stabilising – still higher than the pre-pandemic norm. In addition, the National Living Wage rose by 6.6% to £9.50 an hour last April, coinciding with a hike in National Insurance of 1.25p in the pound for both employers and employees. Such increases in cost can quickly erode margins, leading many companies to look at point solutions where automation can be scaled up over time.
Labour availability
Labour is no longer easily and readily available. Logistics UK reported in late 2021 that more than 13% of businesses were experiencing severe problems recruiting warehouse staff, compared to autumn 2020 when zero respondents recorded such difficulties. Similarly, the UK Warehousing Association recently reported that some warehousing businesses were experiencing vacancy rates of over 20%, with its CEO, Claire Bottle, saying the warehouse industry is ‘tens of thousands’ short in terms of employees.
Uncertainty is a big issue for many businesses using flexible labour. Firms can find that up to 20% of gig-economy labour may not show up, creating significant problems for businesses during critical peak periods. Uncertainty over labour availability can now be a key factor, above cost of labour, in businesses choosing to invest in automation.
Supply anxiety and the great space shortage
Supply issues are a major concern, both in the manufacturing and retail sectors; a combination of the after-effects of a post-pandemic global recovery and complexity arising from post-Brexit customs procedures. Uncertainty over lead-times, deliveries and the supply of parts is hindering planning, impacting production lines and creating gaps on retail shelves. These issues with supply have led many businesses to adopt strategies that enhance supply chain resilience. Consequently, organisations are sourcing goods closer to home and importantly, increasing levels of inventory, leading to unprecedented demand for warehousing space.
In the autumn of 2021, property agent Cushman & Wakefield reported that available space in the UK had fallen below 50 million sq ft, the lowest level since it started tracking availability in 2009.
However, this shortage of space is not a sudden phenomenon, nor a short-term problem, and it has been exacerbated by the steady growth of ecommerce.
A report published in January 2022 by the British Property Federation and Savills finds that demand for warehouse space across England has been underestimated in planning policy for a decade and that future demand is likely to be at least 29% higher than past levels. This chronic shortage of warehouse space has seen rents rise 61%.
With space in such short supply and rents rising, businesses will need to focus on maximising productivity within the cube. However, many businesses are overlooking – or are unaware of – the potential to use readily available technology to drive performance, and hence capacity and growth, from an existing footprint.
The impact of Ecommerce
Ecommerce has radically changed the dynamics of the warehouse. A shift in emphasis away from pallet loads towards single or few-item order picking processes required for ecommerce has dramatically increased dependency on finding sufficient pools of available labour. Until recently, this wasn’t a problem. However, labour is now a scarce resource. Businesses wishing to grow and increase capacity are constrained by the poor availability of labour and the competition from local businesses for those same, limited resources. As a result labour rates are rising.
The pandemic propelled ecommerce to new heights. ONS figures put Internet sales as a percentage of total retail sales at 30.4% in November 2021, a considerable rise on the pre-pandemic peak of 21.6% in November 2019. At the height of lockdown in January 2021 that figure hit 37.8%. And although figures have returned to more modest growth, with shoppers returning to the high street, expectations for ecommerce remain high.
According to a report into ecommerce published in February 2022 by Metapack with Retail Economics, UK retailers are expecting an additional £19.6 billion of online home deliveries by 2025, with online predicted to account for 49.7% of total non-food sales within that timeframe.
Importantly, ecommerce has also given manufacturing businesses the opportunity to sell directly to customers. How these businesses approach fulfilling Internet orders may well play a critical role in determining how successful they are.
The challenge to support growth
Supporting and enabling the future growth of the businesses has become a major challenge for those responsible for fulfilment. Mitigating cost may be a perennial issue for most businesses, but significant structural change within the labour market, following Brexit and the pandemic, together with a constricted warehouse property market – where availability is low and rents high – has placed a great number of companies under intense pressure. How can fulfilment gear-up effectively for growth when labour and space are hard to come by and costs for both are rising sharply.
A growing number of businesses are using smart warehouse automation, such as robots, to drive productivity within the warehouse; reducing exposure to labour issues, mitigating operational costs and significantly increasing capacity. In fact, technology analyst, Gartner, predicts that 75% of large warehouse enterprises will have adopted some form of intralogistics related smart robots by 2026.
Interestingly, the low cost of robot technology now puts it within the reach of SMEs too. Smaller companies have the opportunity to leverage the performance gains created by flexible and easily scalable Autonomous Mobile Robots (AMRs), possibly giving them a competitive advantage over larger companies encumbered by out-dated, inflexible fixed systems.
The rise of the robot
AMRs offer tremendous flexibility and, importantly, scalability in traditional labour-intensive tasks such as order picking and put-away. AMR systems combined with pick-to-light technology can boost order picking performance from under 100 units per hour using traditional methods, to up to 400 picks per hour, with an ROI that can be as little as 12 months.
Mobile robots may also be used effectively to transport pallets, roll-cages and totes within a warehouse, or for sorting parcels, offering a more flexible alternative to fixed conveyor systems. And ‘follow me’ type mobile robots can cut out lengthy time-consuming runs within the warehouse, working as cobots alongside picking operatives. In cold stores too, some AMRs are designed to work in temperatures down to – 25°C and are resistant to condensation – even capable of carrying two roll-cages at a time.
But there are other forms of automation that are also in demand. De-stuffing of shipping containers is a labour intensive task that has many businesses looking for alternative mechanised or automated assistance. Within ecommerce returns operations the speed with which items can be processed and re-despatched can help boost capacity of fast fashion goods, securing more sales and increasing margins. The use of overhead pouch systems can play a major role in buffering high-demand products close to despatch, saving considerable effort returning items to storage.
There is a bewildering array of AMRs and intelligent automation, all with their own specific technical attributes and capabilities suited to particular applications. The problem for those looking to apply this technology is, knowing which is best suited for the task. Important too, is the consideration of the solution as a whole, which may include ASRS systems, automated packaging machines, overhead pouch sorters, pick-to-light technology, powered roller conveyors or a multitude of other technologies.
Specialist knowledge
Under such circumstances, it helps to consult an independent systems integrator. For warehouse storage systems, a skilled integrator can handle everything from concept and design to systems engineering and managing software and hardware requirements efficiently. Not being bound by any one technology or in-house manufactured solution, they are free to be objective about specifying the right solution for the application. Bringing a combination of technologies together in a cohesive way, based on process efficiency and overall performance, is what counts and much of this depends on the software development and the skills of the integrator to successfully tailor the solution for optimum performance.
Flexible technology combined with powerful, intelligent software allows for a new way of thinking. A conventional conveyor system is normally installed to an agreed throughput, usually to a projected peak figure. But this results in the asset running below capacity for the majority of the year. On the quietest day it may only handle a tenth of the volume experienced at peak. However, a solution using AMRs could be designed for 70% of peak, with additional robots brought in during peak periods. It’s this level of scalability that offers SMEs a flexible low-entry point to automation.
Advances in simulation
Simulation software brings a concept to life. For instance, at Invar Group, we have invested in leading-edge 3D simulation technology that enables us to select the most suitable materials handling hardware from a virtual catalogue and place appropriate technologies together as a concept system within the software. Then, by inputting a customer’s real data set, we can apply routing logic to allow us to view its performance and see in advance, any potential bottlenecks in the system.
Testing a concept in this way highlights where in the system there is too much capacity and where there isn’t enough, and hence, where expansion is required. Then you can scenario plan for what ifs, such as twice as many orders, or twice as many products, what if slow movers became fast movers and what happens at peak?
Digital transformation
A business’ competitiveness depends upon its access to, and analysis of, critical data. And smart business will be developing smart warehouses where robots, pickers, packaging machines and sorters are seamlessly integrated to produce, not only optimum performance, but valuable data that is shared in real-time with wider systems in order to deliver competitive advantage.
It is the efficient integration of these processes, technologies and intelligent software that enables fast delivery of a solution and a trouble-free future. An intelligent system, conceived by expert design engineers and implemented by competent controls and software professionals, drives productivity and offers the agility needed to respond to change.
As an independent, full-spectrum automated warehouse solutions provider, Invar Group is free to select the most appropriate technology for the task, and being a multifaceted organisation that brings together skilled individuals with competencies across warehouse management software, systems integration and controls, we take responsibility for the complete turnkey-key system from start to finish.
You might also like
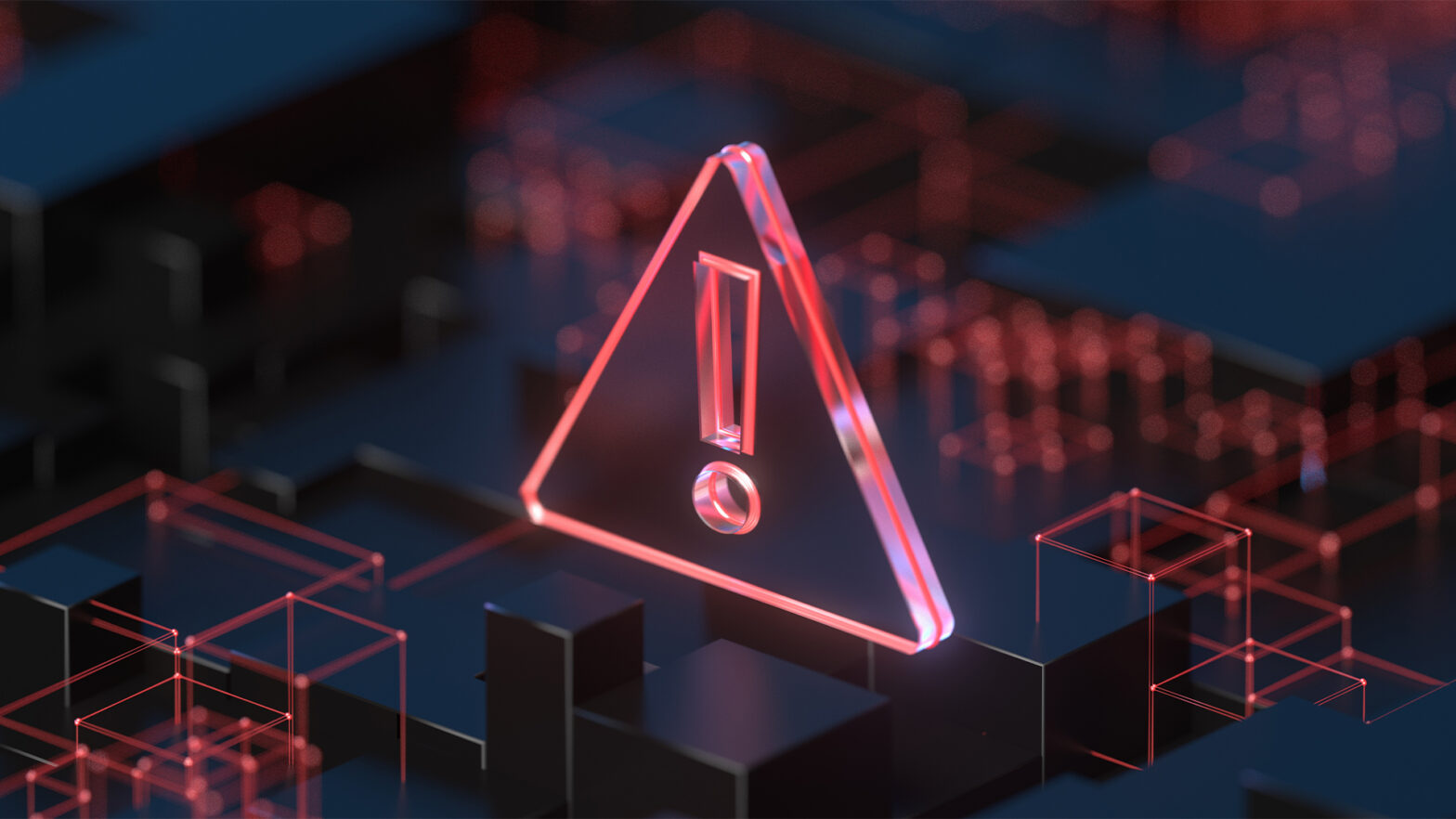
Technology
25 March 2025
Ransomware-As-A-Service Variants on the Rise With Critical Infrastructure Providers at the Greatest Risk
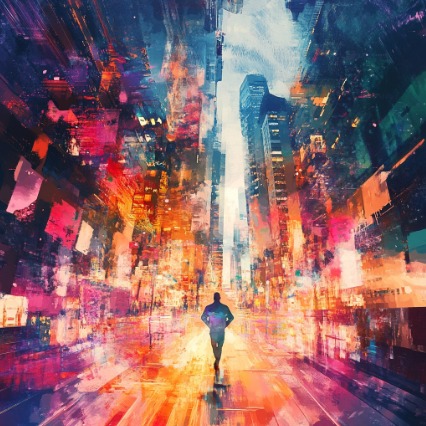
Business Advice
25 March 2025
Claims Processing Automation: How Insurers Can Cut Costs and Improve CX
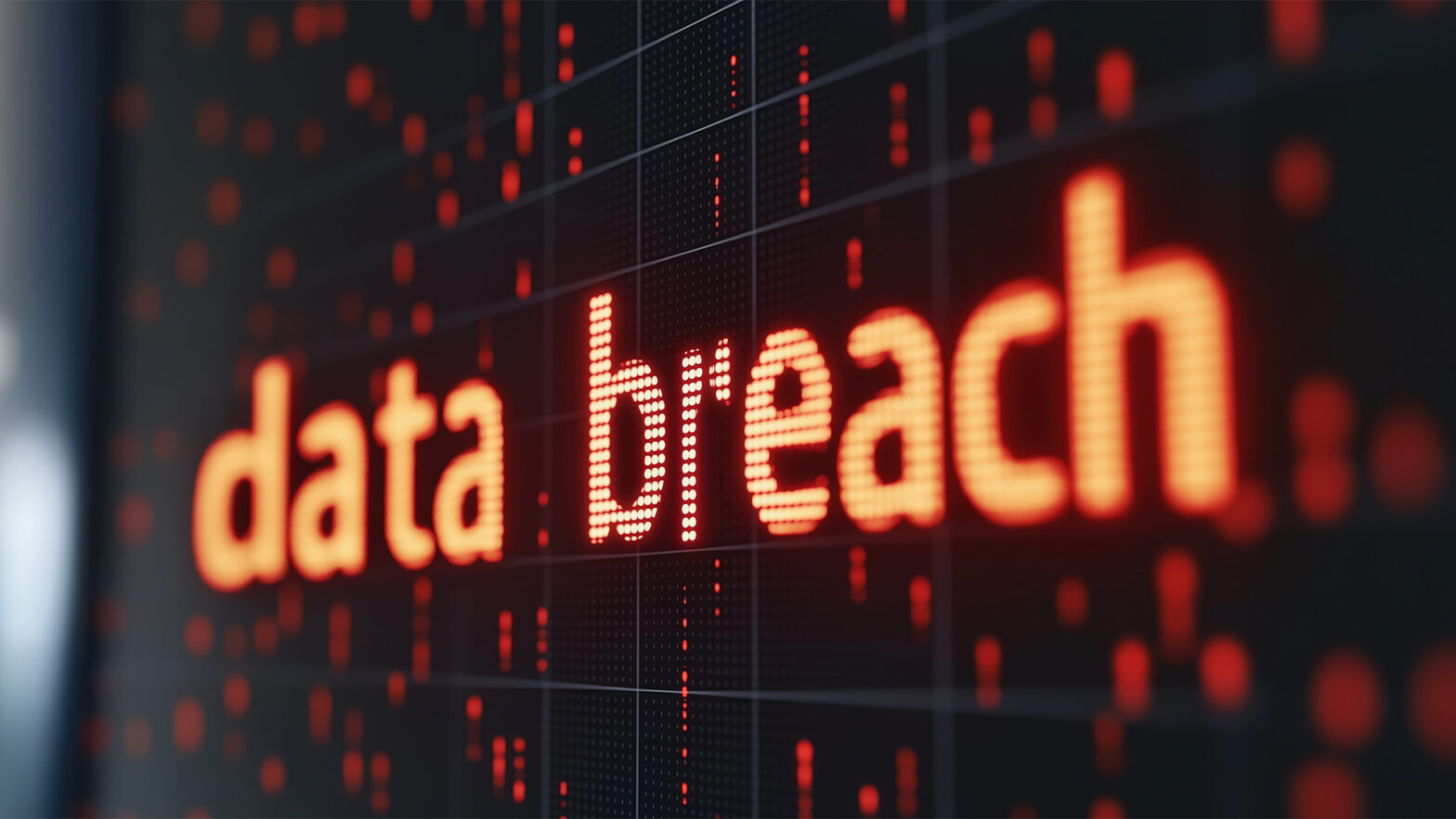
Technology
18 March 2025
Secret Signs Your Internet Security Has Been Compromised